Case study
A perfect package - Chillers cool down injection moulding machines at competence center
Injection moulding requires very high temperatures, and the workpieces must be cooled down immediately after moulding. Chillers tailored to the needs of specific applications are particularly suitable for the demanding task of cooling injection moulding machines. Chiller configuration precisely matched to the required cooling capacity is necessary to avoid underdimensioning or overdimensioning of the chiller. A good example of what a tailored package solution looks like is the Pfannenberg chiller installed in the test lab of PolymerEngineering in Hamburg, Germany.
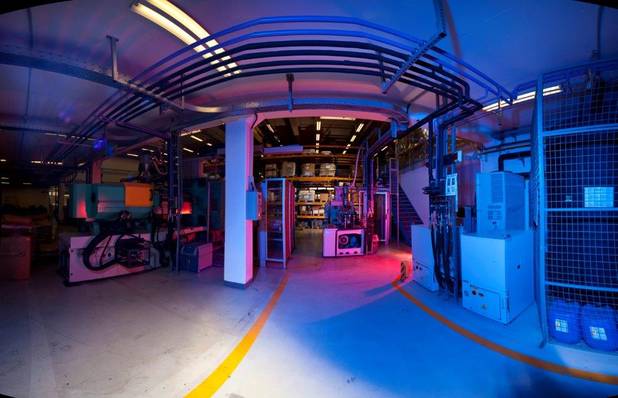
The competence centre PolymerEngineering belongs to TU Tech Innovation GmbH which deals with the continued development of thermoplastic polymers. The PolymerEngineering team develops applicationspecific solutions, for example they optimized the heat management of high-capacity LED components through direct back-moulding of heat conductive synthetic resins.
Wanted: a package provider
For the construction of a competence centre for polymer research in Hamburg-Wilhelmsburg, PolymerEngineering was looking for a regional partner for the effective cooling of injection moulding machines and tools used. Along with supplying the necessary equipment, their ideal partner would also be able to handle maintenance and installation. They found what they were looking for in Hamburg-based Pfannenberg, a specialist in cooling solutions. The first phase of the project involved water cooling of three injection moulding machines. Despite different basic conditions, the objective was to cool all three machines with a single chiller. In order to determine the right chiller for the job, Pfannenberg’s experts first analysed the local conditions and calculated the actual cooling demand as well as the required supply temperature. If it is only when the capacity of the chiller is optimally adjusted to the application, that is the only way to ensure smooth operation of injection moulding machines. Otherwise, with overdimensioning, there is the risk of higher electricity costs and reduced lifetime of the chiller, or of outages and costly downtime of the injection moulding machine(s) with underdimensioning.
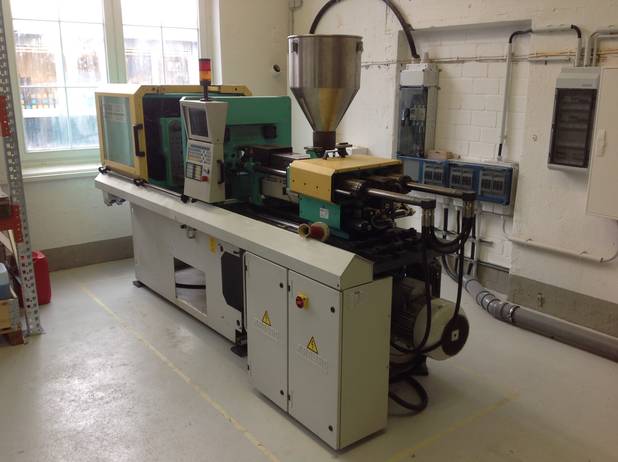
Without the cooling provided by the Pfannenberg chillers, it basically would not be possible to operate the injection moulding machines. We are pleased that in Pfannenberg we have found a regional partner which is not only able to deliver quickly, but also provides all necessary services from a single source.
Systematic water cooling
Now an EB 130 WT CE STD chiller with a cooling capacity of 12 kW at a maximum ambient temperature of 35 degrees is cooling the injection moulding processes of three injection moulding machines from various manufacturers, including Battenfeld and Arburg. The volumetric flow rate is 10 litres of water per minute, with the supply temperature held to a fixed value of 20°C. Configured specifically for this application, the chiller is additionally equipped with a hydraulic bypass. Pfannenberg provided the full scope of services, from design and on-time delivery to commissioning, including three-phase power measurements, functional testing and assistance in piping installation. After-sales maintenance is also part of the package.
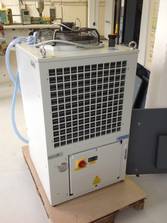
Everything from the same source
“Without the cooling provided by the Pfannenberg chillers, it basically would not be possible to operate the injection moulding machines”, says Sven Polatzek, project manager at PolymerEngineering. “We are pleased that in Pfannenberg we have found a regional partner which is not only able to deliver quickly, but also provides all necessary services from a single source.” The synergies go even further. Firstly, Pfannenberg ensures the required process reliability for injection moulding. In exchange, PolymerEngineering can provide advice on injection moulding to companies which use injection moulding machines in their production facilities for filter fans and signaling devices. PolymerEngineering also presents seminars on injection moulding. Seminar participants can learn how process cooling works, based on actual systems as examples. Along with the chiller, as a technology partner Pfannenberg also provides filter fans and signaling devices to indicate the operating status of the machines.
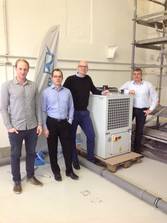
Summary
Pfannenberg is the only manufacturer to offer a “Total Worry-free Package” for process cooling which along with supplying a range of different cooling devices includes advice, application-specific configuration, installation and maintenance. One important point is the close collaboration with the customer (preferably, right from the planning process), to meet the customer’s specifications, in that case to provide one single chiller to cool down three different kind of injection moulding machines. The first innovation center for polymer engineering in the north of Germany can now count on Pfannenberg as a local and competent partner, experienced in liquid cooling solutions.
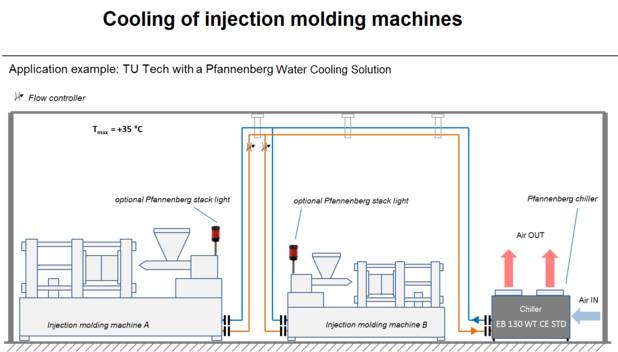
Facts at a glance
Task
- Efficient cooling of several different injection moulding machines, which need to be coincide perfectly with each other
- Regional partner with full-service competence
Challenges
- Dimensioning together with customer
- Full support from dimensioning to installation of piping system
- Commissioning incl. functional testing, check of rotary field, etc.
- Service and maintenance (even of third-party devices
Technique applied
- Chiller EB 130 WT CE STD with 12 kW cooling capacity
- Signal tower BR 50 (XENON)
Success Factors
- Service: everything from a single source – from dimensioning to installation/maintenance
- Local support by local supplier
- Prompt delivery
描述 | 語言 | 类型 | 大小 | 下载 |
---|---|---|---|---|
Case Study Polymer Engineering |
|
340 KB | 下载 |